Transformacja Lean – od czego zacząć? Które narzędzia są najlepsze, aby rozpocząć skuteczne zmiany?
Jakie pierwsze cele postawić konsultantom?
A może iść do gemba i zacząć od małych kroków, doskonalić proces wspólnie z operatorami, specjalistami operacyjnymi, bo przecież są najbliżej problemów.
Może więc bezpiecznie, zacząć od nieśmiertelnego 5S „na rozruch”? A może SMED, mamy w końcu tyle przezbrojeń? Może jednak od razu wynająć konsultantów. Niech zrobią mapowanie procesu, spojrzą na proces” z boku”, pomogą opisać problemy?
Takie pytania powtarzają się na forach specjalistów Lean od zawsze. Zadają je sobie zespoły w firmach, przygotowujące pierwszą i kolejne projekty transformacji Lean.
Niestety, zbyt często, zapał i koszty wdrożenia przepalane są na ważnych, ale nie mających wpływu na istotne zmiany w procesie, obszarach, narzędziach doskonalenia i kierunkach strategii zmian.
Tymczasem proces produkcyjny, pomimo całej swojej złożoności, ma tylko dwie istotne składowe:
- strumień procesów,
- wąskie gardło/ograniczenie procesów
I jeden cel:
- zapewnienie ciągłości przepływu procesów.
Wszystko to po to, aby klient mógł nam jak najszybciej zapłacić za towar, bo, szybki obrót to:
- płynność finansowa,
- niskie (niższe niż konkurencja) koszty operacyjne,
- i zysk z działalności operacyjnej
(co wcale nie oznacza jeszcze rentowności, ale to szerszy temat).
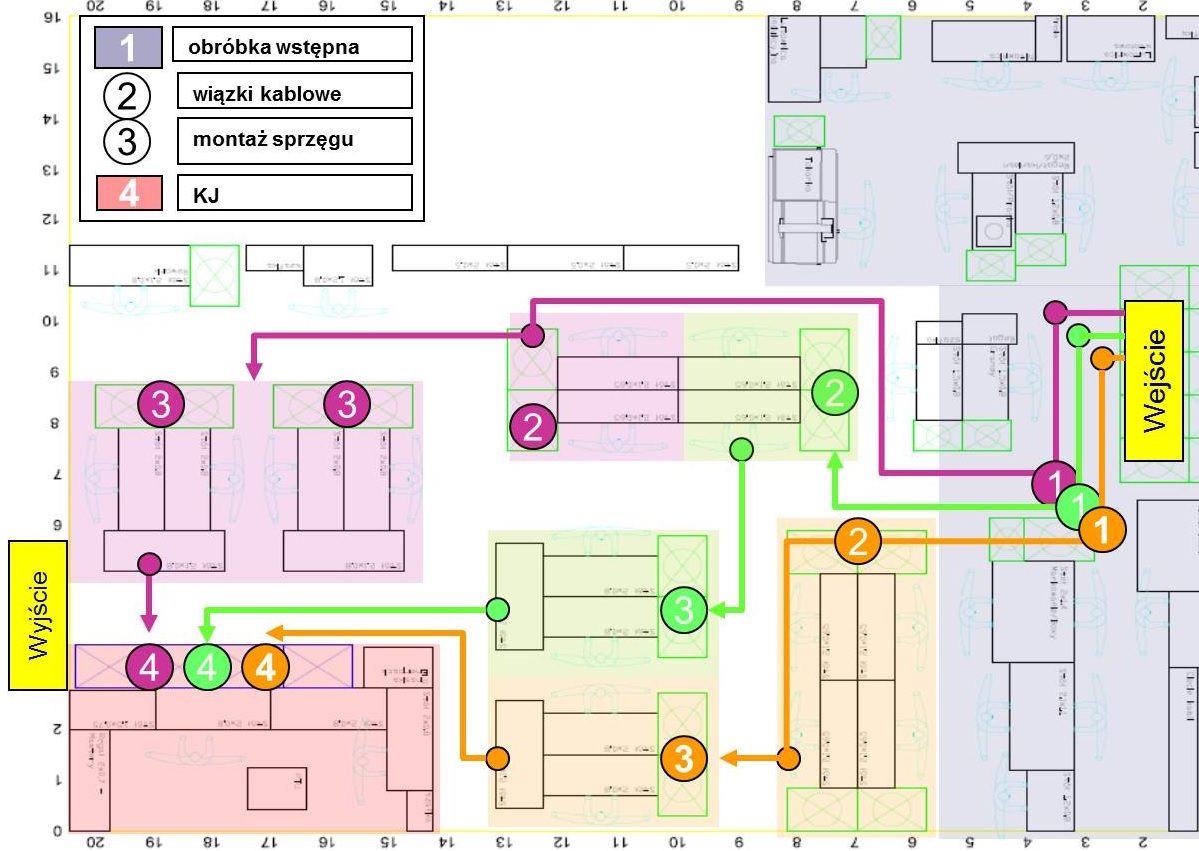
Czy to oznacza, że wszystkie narzędzia Lean, od których tradycyjnie zaczynamy wdrożenia są niepotrzebne?
Wręcz przeciwnie-są niezbędne i bez nich projekt transformacji albo się nie uda, albo będzie niepełny.
Trzeba je tylko użyć w odpowiednim momencie inaczej będzie to MUDA Niewłaściwej Metody.
Toyota, według mnie, zdefiniowała 7 Marnotrawstw / Muda nie po to, aby uczynić z inżynierów łowców MUDA, ale po to, aby dać im wskazówki, gdzie szukać problemów, jak je nazywać i z czym łączyć. To element Standaryzacji, a nie cel sam w sobie.
Celem jest przepływ, a wręcz JIT.
Nie zobaczymy JIT w mniej lub bardziej wyczyszczonym i zmodernizowanym zakładzie.
Nie zobaczymy go także w większości nowoczesnych systemów wspomagających.
Natomiast o przepływie, a najbardziej o jego braku, powiedzą nam:
- wąskie gardła, zastawione produkcją w toku,
- i wiecznie spóźnione montaże i kompletacje, czekające na części.
A to na jakie podzespołu czekają najczęściej nasze procesy, może być wskazówką, gdzie szukać „początku naszej drogi Lean”.
Tu oczywiście niska jakość może nas wywieźć na chwilę w pole, ale eliminować nieakceptowane przez klienta wady warto i należy zawsze. Niedociągnięcia na tym polu to nokaut. Nieefektywność to tylko przegrywanie na punkty.
Jak więc zacząć wdrożenie, żeby nie zmarnować czasu na sprzątanie i usprawnianie obszaru, który być może przebudujemy lub całkowicie zreorganizujemy? Które narzędzia dostarczą najważniejszych informacji na start?
IDŹ do GEMBA
Oczywiście rozpoznanie to pierwszy krok każdego mądrego lidera. Tyle, że sama obserwacja poda nam co najwyżej poszlaki przyczyn problemów i pozwoli policzyć potencjały do odzysku.
To jednak akurat element propagandy, o który jednak warto zadbać, by pozyskać sojuszników i sponsorów naszej zmiany-Dyrekcję, szefów wydziałów. Oni muszą dostać trochę twardych danych, że zmiana będzie się opłacać.
Narzędzi do wyliczenia MUDA jest dużo – szkoda na to czasu w tym artykule.
Co więc obserwować?
Opisz Przepływ
Opisz przepływ procesu i kroki technologiczne/marszrutę wytwarzania:
- jak się odbywa,
- które stanowiska obejmuje,
- czy płynie czy krąży i zawraca produkty na wcześniejsze stanowiska,
- czy jest naprawdę realizowana, czy pracownicy już od dawna pracują tak żeby się dało, a nie tak jak się w biurach technologom wydaje.
Narzędzia:
- nawet prosty diagram blokowy,
- wybrani reprezentanci produktów,
- i pisak do robienia strzałek, a dla bardziej zaawansowanych i wyrafinowanych, Excel oraz jego narzędzia graficzne, gdzie w zakładkach zbierzemy wszystkie dane, tworząc bazę projektu w jednym pliku.
To, co z tego wyjdzie, będzie trochę przypominało Diagram Spaghetii, ale w Spaghetii chodzi o Muda, a nam chodzi o proces. Muda nic tu nie zmieni.
Zmierz Przepływ Procesu
Gdy już wiesz jak naprawdę płynie proces to wyrobisz sobie zapewne także opinię, a raczej przeczucie tego, z czym ludzie na produkcji codzienne się mierzą. Prawdopodobnie zauważysz kilka nieracjonalnych przepływów, które nie mają uzasadnienia, ale teraz są niezbędne i nienaruszalne.
Prawdopodobnie dostrzeżesz wąskie gardła. Tak – świadomie piszę w liczbie mnogiej.
Może być ich kilka w jednym obszarze, gdy:
– wykonujesz kilka różnych modeli wyrobu o innej konstrukcji,
– wykonujesz różne produkty, różniące się operacjami i czasochłonnością.
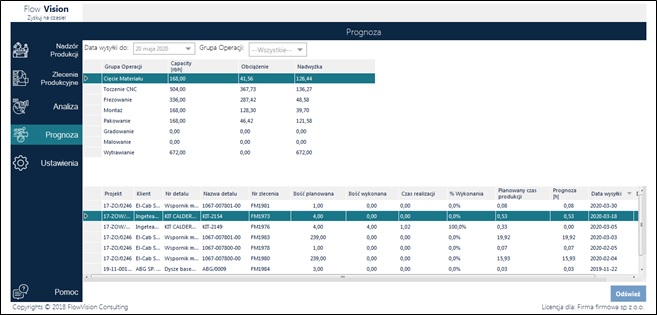
Co więc teraz zrobić? W myśl naszego motta na tym blogu „Kto nie mierzy, ten nie zarządza” – Musimy zmierzyć proces.
I to dla każdego reprezentanta grup produktowych.
Jak to zrobić? Sposobów jest kilka:
– raport operacyjnych czasów rejestrowanych na każdym stanowisku i operacji marszruty z MES, z zestawem zmierzonych czasów (analitykę można wykonać w Excelu, no chyba że zawiera ją MES, ale raczej nie),
– gdy nie mamy, wystarczy prosta tabelka w Excelu, wydrukowana na kartce w intensywnym kolorze, pozwalająca na zebranie czasów rozpoczęcia i zakończenia operacji wraz z uwagami o zakłóceniach
(Dla Uważnego Czytelnika: jeżeli potrzebujesz szablonu napisz maila lub poproś w komentarzu ).
Co nam to da?
Pozwoli wykorzystać kolejne narzędzia:
- Yamazumi (poziomowanie produkcji),
- rozszerzyć schemat blokowy procesów operacyjnych dla reprezentanta przepływu o analizę przepływów fizycznych,
- wskazać wąskie gardło, zaprojektować jego eksploatację i wzmocnienie, zaplanować bufory.
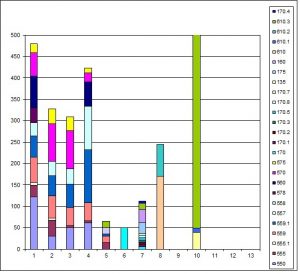
Stąd już tylko krok do książkowego i dobrze przygotowanego BigPicture i warsztatu Curent/ Future State.
To jak przeprowadzić powyższe analizy, jeżeli jeszcze tego nie robiłeś, warto zapytać i zaangażować znajomego konsultanta. Warto też spróbować przeprowadzić proces samemu.
W tym artykule poprzestanę na wskazaniu kierunku, gdyż każde z narzędzi zasługuje na odrębny artykuł i jeszcze nie wyczerpie tematu. Za to wdrożenie i zobaczenie, zmierzenie zależności to niesamowita satysfakcja „odkrywania” procesu, do czego zachęcam.
„Nauczyć się widzieć” to sztuka, która przychodzi z czasem. Wspierajcie się narzędziami jak systemy MES. To nie musi kosztować majątku, ani nie sparaliżuje organizacji wdrożeniem (choć potrafi).
Natomiast na początek Transformacja Lean potrzebuje kartki, excel i otwartych oczu oraz głowy.