Lead time (L/t), czyli czas przejścia produktu przez proces, to obok ceny i jakości, najważniejszy miernik dla klienta.
Dlaczego? Jestem przekonany, że każdy logistyk, zakupowiec, a przede wszystkim kierownik produkcji nie ma co do tego wątpliwości. Dla klienta Lead time to wskaźnik oczekiwania na towar.
Jak często czekaliście jak na szpilkach na dostawę ostatniego brakującego podzespołu, wstrzymując cały montaż i ustawiając go w gotowości do natychmiastowego pobrania części, zakończenia projektu i wysyłki do waszego klienta.
Dla producenta Lead time jest równie ważny, a wręcz kluczowy. Niestety, bardzo często lekceważony i niedostrzegany. Nasze skupienie na ciągłym poganianiu produkcji w poprawianiu wydajności powoduje, że odrywamy się od rzeczywistości całego strumienia.
To właśnie Lead time mierzymy na mapie Big Picture podczas mapowania strumienia wartości. To właśnie w oparciu o wykres tego miernika odczytujemy zakresy czasu czynności dodających wartości (VAA) i czynności nie dodających wartości (NVAA).
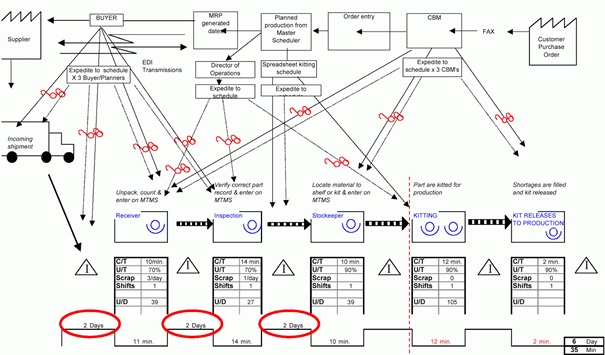
Od pomiaru czasu przejścia już tylko krok do pomiaru Efektywności Strumienia czyli Produktywności i Marnotrawstwa, jako jego przeciwności:
Efektywność Procesu = [Wd (wartość dodana) / Lt (lead time)] x 100%
Przykład :
– Produkujemy „Bułkę z serem”
– Obserwacja Procesu:
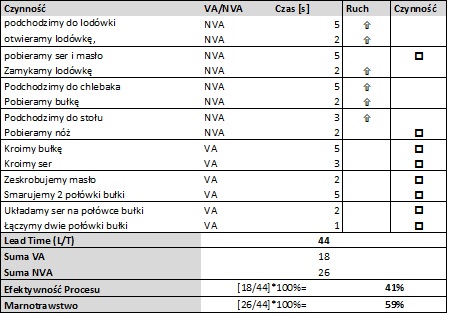
Oczywiście, wszystko to przy założeniu, że jest to nasz jedyny proces.
Ilu dyrektorów i kierowników odpowiedzialnych za produkcję naprawdę rozumie ideę Big Picture?
Jak wielu naprawdę rozumie swoja rolę i odpowiedzialność za spoglądanie z góry na cały proces? Czy może zamiast tego wchodzą w, często nieistotne, lokalne zakłócenia i dyskusje o OEE czy innych miernikach operacyjnych?
Dla lepszego zobrazowania zależności związanych z Lead Time poniżej zestawię te parametry procesu, które są z nim bezpośrednio lub pośrednio związane.
- Czas Przejścia – czyli podstawowy parametr, L/T obrazuje ile czasu potrzebuje produkt, aby przejść wszystkie etapy procesu, uwzględniając procesy operacyjne oraz składowanie, które traktujemy jako marnotrawstwo,
- Wartość Dodana i Marnotrawstwo – analizując czas przejścia przeprowadzamy pierwszą i najszybszą analizę wartości dodanej naszego procesu, to właśnie analiza Lead Time pierwsza pozwala wykryć miejsca, gdzie produkt zamiast płynąć zatrzymuje się i rozpoczyna się Muda Oczekiwania /Składowania, dodatkowo łatwo wykryjesz Marnotrawstwo Transportu,
- Marnotrawstwo Oczekiwania – L/T obrazuje zakres czasu efektywnie wykorzystywanego w strumieniu lub jego fragmencie. Tym samym, na zasadzie przeciwności, wskazuje udział oczekiwania/składowania produkcji w toku, ale też informacji. Staje się miernikiem rotacji materiału i wkładu pracy, czyli wartości dodanej.
- Opóźnienia Dostaw (On time delivery OTD) – wiedza o czasie przejścia jest kluczem do określenia terminu dostawy, jeśli go nie znamy zgadujemy zamiast pracować na faktach, dla klienta OTD to wskaźnik naszej wiarygodności i podstawa własnego planowania,
- Efektywność – jest miarą sprawności procesu, L/T możemy odnieść do całego strumienia lub jego części, analizując jego fragment. Tym samym Efektywność produkcji jest zwykle wyższa od jej przygotowania, gdyż w umownych biurach, projekty zwykle czekają.
- Miernik zamrożenia kapitału – L/T obrazuje jak dużo czasu firma mrozi swój kapitał realizując każdy cykl produkcyjny danego produktu i projektu, czy w efekcie ile nas ten kapitał kosztuje.
- Model struktury zapasów – L/T pozwala na określenie miejsc i wielkości zapasu liczonego w dniach i stopniu przetworzenia.
Oczywiście pod warunkiem, że potrafimy to zmierzyć. Doskonałym źródłem klasycznej wiedzy na temat analityki procesu dostarczył pan John Shook w podstawowej dla każdego Lean’owca książce “Learning to See”. Lead time pomaga patrzeć. Oczywiście obecnie możemy się już także wesprzeć wsparciem komputerowym, o czym kilka słów niżej.
Jak mierzyć Lead Time?
Co do zasady metoda jest prosta:
– wybierasz produkt,
– wybierasz zlecenie produkcyjne, które go realizuje,
– zapisujesz datę i godzinę rozpoczęcia operacji z nim związanej (najlepiej zrobić sobie tabelkę i zapisywać daty/godziny operacji na każdym stanowisku),
– to samo zapisujemy dla końca operacji.
Proste. Mamy cały czas przejścia, wraz ze wszystkimi międzyczasami.
Dodatkowo uzyskujemy czasy oczekiwania pomiędzy operacjami i zaraportowane czasy każdej operacji . Praktycznie proces w pigułce.
Są tylko dwa problemy:
– nadzorowaliśmy tylko jeden wyrób (nawet jeśli to teoretyczny reprezentant grupy), a możemy mieć kilkanaście innych, o których nic nie wiemy,
– całą pracę analityczną oraz zapisy zrobiliśmy ręcznie, a informacja dotarła do nas wówczas, gdy nasza tabelka („czerwony kanban”) przeszła cały proces.
Jak dużo takich tabelek jesteśmy w stanie przepuścić przez procesy? Ile z nich damy radę przepisać do excela? A co zrobimy, jeśli coś się zmieni? Jak się o tym dowiedzieć?
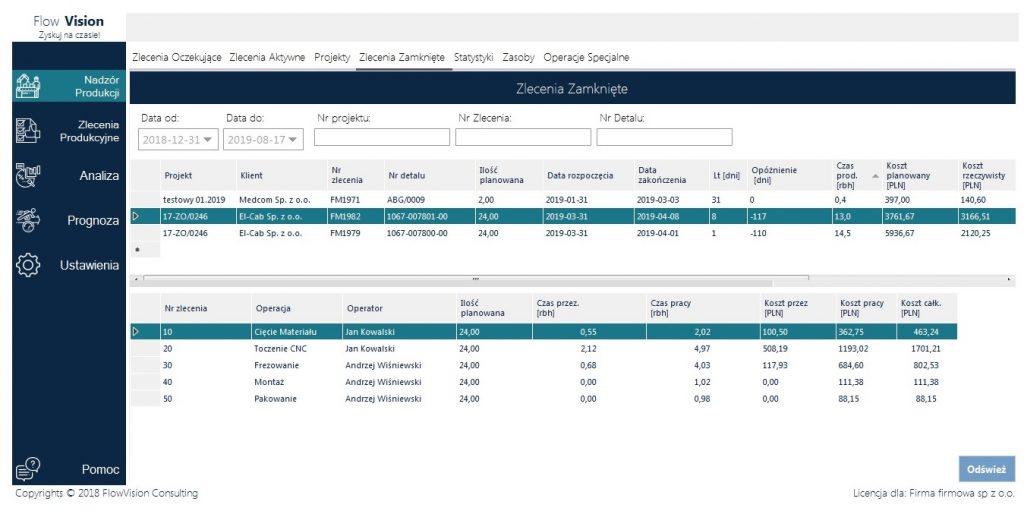
W całkowicie wystandaryzowanej produkcji temat załatwią Karty Zlecenia z normami. Odchylenia zostaną skorygowane dzięki codziennym spotkaniom wydziałów przy Tablicach Rozwiązywania Problemów.
Ale co z nieśmiertelnymi firmami o „niepowtarzalnej specyfice” i „niepowtarzalnej produkcji”? Jest sens to mierzyć? Według mnie przede wszystkim w takich firmach warto mierzyć Lead time. Dla krótkoseryjnej produkcji Lead time, jego etapy operacyjne i marnotrawstwo oczekiwania, stają się wyznacznikami kosztów i postępów projektu. Nie ma chyba tańszego miernika do zarządzania projektem i zleceniem niż Lead Time.
Lead Time – pomiar automatyczny (MES).
Oczywiście nie zachęcam nikogo do rozbudowy biurokracji, choć sam tak robiłem. Alternatywą jest nie nadzorować nic, co robi wiele firm, lub podejmować akcje, gdy problemy z rentownością i dostępnością zasobów zaczynają boleć prezesów.
Jest to blog o ułatwianiu sobie pracy poprzez systemy automatyczne. Stad będę namawiał do wykorzystywania systemów MES do bieżącej kontroli postępów i reagowania na odchylenia w skali statystycznej, ale możliwie natychmiast po ich wystąpieniu, a nie po zakończeniu produkcji.
Większość systemów MES mierzy Lead Time całkowicie automatycznie. System raportując czas rozpoczęcia i zakończenia zlecenia łatwo wyliczy Lead Time dla każdego produktu. Łatwo też wskaże dodatkowo:
– czasy etapów produkcji,
– czasy przestojów,
– oraz poziom marnotrawstwa.
MES zlicza czasy operacyjne z dokładnością do zlecenia i produktu, natomiast raport zbiorczy da nam wiedzę statystyczną niezbędną do oceny reprezentantów strumieni i przygotowania Big Picture.
Czy da się to zrobić i nie wdać się w wieloletnie i kosztowne wdrożenie?
Twierdzę, że tak. Tak prosty miernik jak czas przejścia, system MES zmierzy bezproblemowo. To przecież tylko różnica dwóch dat. Dodatkowo zrobi więcej – zmierzy każdy Lead time, każdego przejścia i każdego produktu. Dla dociekliwych, odpowiedni raport, będzie pokazywał miejsca , czas i wielkość zapasów, zatrzymanych pomiędzy operacjami. Natychmiast dowiesz się, czy zarobiłeś na zleceniu czy też nie.
Technologia jest dostępna. Nie wymaga też rewolucji, ani potężnych inwestycji, choć takie rozwiązania dominują. Twój Lead time może się zmniejszyć, a wraz nim marnotrawstwo czasu w procesie i koszty. Czas jest najważniejszy. To na nim opiera się cale doskonalenie w Lean. To czas jest walutą, którą tracąc, nigdy nie odzyskasz.
Proszę nie odnosić wrażenia, że się czepiam, jednak nie do końca zgadzam się z tezą tego artykułu. System, na przykład MES, może być do pewnego stopnia pomocny przy zbieraniu danych do Mapy Strumienia Wartości, a konkretnie – do obliczenia L/T, jednak nic nie zastąpi bezpośredniej obserwacji. Przyczyn można by wymienić wiele, podam tylko najważniejsze, oczywiście moim zdaniem. Czynnik ludzki. Ludzie to nie maszyny, nie działają tak, jak systemy zamknięte. Cały czas nawiązuję do sposobu wprowadzania danych do systemu. Wiele działań operacyjnych, maszyn, nie posiada automatycznego sprzęgu z systemem, np. MES. Samo odnotowanie “startu” i “stopu” danego procesu, np. dla wybranej rodziny produktów, pozwala jedynie odnotować sam czas przejścia, z czasami VA i NVA jest już znacznie gorzej. I rzecz dla mnie zasadnicza: tworzenie VSM / Big Picture nie musi być precyzyjne. W tej technice obrazowania procesu (stosuję ją bardzo często) chodzi po prostu o uchwycenie tego ‘dużego obrazka” oraz zidentyfikowanie, gdzie powstaje marnotrawstwo, jakiego typu, a przede wszystkim gdzie są wąskie gardła. Należy pamiętać, że tworzenie Map Strumieni Wartości jest działaniem dodatkowym (Muda Typ I), koniecznym, ale nie dodającym wartości. Jest pomocą w dobrym planowaniu, i dlatego powinno się mu poświęcać tylko tyle czasu i uwagi, ile to konieczne. Tu stosuje się zasada Pareto: jeżeli mogę osiągnąć 80% oczekiwanego rezultatu angażując w to działanie 20% zasobów, to jest to właściwe podejście. Pozdrawiam
Bardzo dziekuje za tą opinię.
W najmniejszym stopniu nie odnoszę wrazenia czepiania się. Mało tego, uważam, że artykuł wręcz jest uzupełnieniem pana doświadczeń i praktyki.
Systemy komuterowe-jakiekolwiek, to tylko wsparcie.
Każdy, kto sądzi, że to one wykonają za niego pracę na hali jest w potężnym błędzie i srogo za to zapłaci-w gotówce, straconym czasie i zniechęceniu załogi.
MES ma zbierać, liczyć i zestawiać dane z różnych etapów i miejsc procesu, wiązać oraz wizualizowć. Ma robić to co sami jesteśmy w stanie zrobić podczas mapowania, ale to czasochłonna praca i trudno ją wykonywać w cyklach ciągłych.
Natomiast jakąkolwiek wartość wszystkie te informacje mają tylko wtedy, gdy codziennie pracujemy na nich z pracownikami w gniazdach, gdy korzystają z nich technolodzy i kosztorysanci, gdy pracuje na nich jakość, pracownicy dostają szybki feed back i wiedzą, ze on się pojawi, zaś klient nie musi być okłamywany bzdurami o stopniu zaawansowania jego zamówień, wyciąganymi z sufitu działu sprzedaży.
Jak z każdym narzędziem – można zrobić dużo albo nic. Konstrukcja MESa tez jest wazna. Pracowalem na kilku, albo raczej byly tam gdzie pracowalem, bo ostatecznie pracowalem na Excelu. Stad FlowVision zaprojektowalem już dla siebie, ale to nadal tylko narzędzie.
Nadal trzeba isc do Gemba i pracowac z ludzmi.
Dziekuję za cenne uwagi, chetnie rozszerzę tą wymianę doświadczeń.
Ja również dziękuję za zrozumienie i ciekawe uwagi. Moje “czepianie się’ wynika także i z tego, że staję ostatnio wobec dylematów, jakie rozwiązania wspierające (IT) polecać w firmach, którym doradzam. Problem, na najwyższym poziomie abstrakcji, wygląda następująco: co robić “ręcznie”, a co wspierać przy pomocy rozwiązań systemowych (IT). To jest problem niebanalny, biorąc pod uwagę zmienność sytuacji biznesowej, potrzeb klientów tych firm, zmian asortymentowych, a często nawet poważnych zmian technologicznych. Pozdrawiam